How To Minimize the Risk of Hydraulic Cylinder Contamination
Keep Your Equipment Running Longer
In the world of hydraulics, hydraulic cylinder contamination can leave a business in a bad place. Contamination can cause hydraulic cylinder failure, putting an abrupt stop to any work that had been getting done and maybe even stopping your operations as a whole. There are many causes of hydraulic contamination and even more reasons to do your best to prevent it from happening right away. Most hydraulic equipment owners understand the importance of keeping their hydraulic fluid clean and clear of debris to reduce the chances of premature failure of their equipment, yet hydraulic contamination remains a big issue for many business owners. Read on to learn some of the ways that you can minimize the risk of hydraulic cylinder contamination and keep your equipment running longer and more efficiently.
First thing first, when it comes to minimizing the risk of hydraulic cylinder contamination, it is important to identify all the different ways that your hydraulic cylinders can become contaminated. This will hopefully help you understand contamination as a whole and how each different contaminant can affect your system.
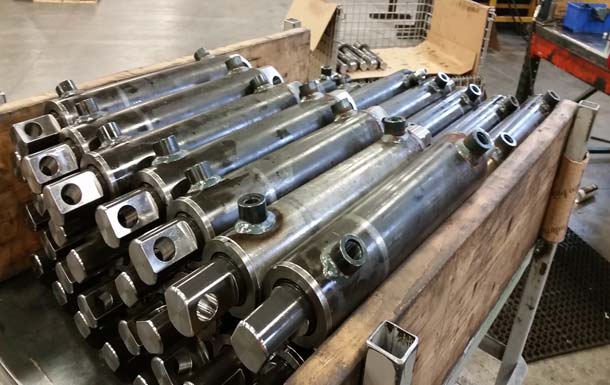
Forms of Hydraulic Cylinder Contamination
Air
When a foamy substance is formed in hydraulic oil, air contamination has occurred. This can affect compressibility, and depending on the amount of contamination that has occurred, it can affect the efficiency of the whole machine. It can impact cycle times and reduce torque. Make sure to keep the system sealed when you aren’t working on it to minimize the chance of exposure.
Built-In
Built-in contamination is by far the least avoidable form. All equipment is contaminated in some way due to the manufacturing process. Metal shavings, weld spatter, fine granules, and threads/fibers form from both the manufacturing process and the environment. When getting a new system, it is recommended to flush it out fully as well as get a great quality filter to get rid of the built-in contamination.
Ingressed Particulate
Ingressed particulates include metal, dust, & dirt that can cause some serious contamination when it comes to your machines. Some of them can be created during grinding, welding, or machining, and others, such as dust and dirt, can just become an issue from a dirty environment (which cannot always be avoided) These particles can cause abrupt and serious damage to your machines because they are known to clump up within the oil. They can also cause cuts and destruction to the sea, which can be a serious issue.
Chemical
Over time, all chemicals degrade, and that is no different when it comes to hydraulic fluid. This is the second most common reason for contamination. Both excess pressure and excess heat contribute to this process occurring. The other way that chemical degradation can happen is from mixing hydraulic fluids. Manufacturers have different blends, which have different additives, and if you use an incompatible combination, contamination happens. Following the guidelines from the manufacturer, as well as using an oil analysis plan, will help reduce the chances of chemical contamination.
Generated
While operating and moving components, wear and tear happen to the machinery. Metal, dust, and fragments take a toll on surfaces and joints, especially if there is a lack of lubrication. Generated contamination usually occurs when new equipment is being broken in, or getting restarted, or even when new parts are added. As your equipment runs and functions regularly, contamination builds up and can negatively affect the efficiency of the machinery. Be sure to check the equipment often, and change filters to limit chances of contamination.
Water
Hydraulic cylinders are powered by hydraulic fluid, which does not have a good reaction to water. Water can contaminate your hydraulic cylinder when your machine is exposed to a humid environment or when parts are not fully dry after they have been taken for cleaning. Water can reduce the amount of lubricant that is required for the system and turn into sludge. It can also cause oxidation and corrosion, which can create irreversible damage to the machinery. Prevent water contamination from happening by keeping the equipment and fluid sealed and secure.
After understanding the different types of contamination that are most common, it’s important to be aware of contamination and where the source is so that you can do your best to prevent it. Within the assembly process, some processes are necessary, and the chances of contamination are higher, but there are certain ways to minimize the risk of contamination.
– Keep work and storage locations clean
– Parts, once clean, should be kept in sealed containers to keep dust, dirt, and particles off before reassembly
– Be intentional with air filters and keep your area climate-controlled
– Invest in lint-free rags and other tools to keep your shop as particle-free as possible
Hydraulic Cylinder Contamination: Conclusion
If you are only a hydraulic user, utilizing filters within your hydraulics will be one of the most important things that you can do to prevent hydraulic cylinder contamination. Various filters can and should be used to help minimize the risk of your hydraulics becoming contaminated. Filters help sift through the hydraulic fluid in your components and catch any debris that could cause an issue in the future. They are very important to use and utilize correctly.
All in all, hydraulic cylinder contamination isn’t something that can always be avoided – but there are ways to minimize the risk and help your hydraulics run for longer through specific care & instructions. If you are interested in learning more about All Phase Hydraulics and how we manufacture and repair hydraulic components, please contact us today! Our team is happy to help you in any way that we can.